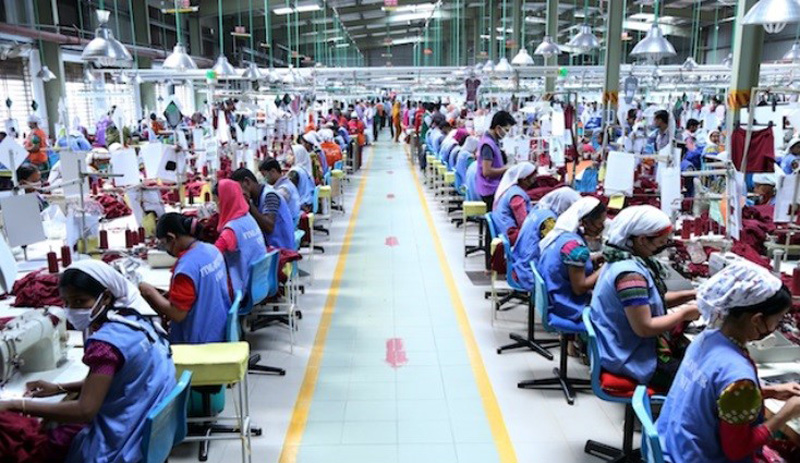
Low productivity. Learn in detail.
Low productivity is a significant obstacle for the garment sector in Bangladesh. Need to Identify the root causes and impact of this issue and possible solutions. The garment industry is the largest export-oriented industry in Bangladesh. The garment industry is best known as RMG (Ready Made Garments). Bangladesh is the second-largest apparel exporter globally. Garment exports to record $47.38 billion in 2023. It is becoming challenging to adjust labour costs in the global market, where the price of ready-made garments is gradually reduced. Because the cost of living for workers, the standard of living, and the cost of production are rising at an abnormal rate. In this scenario, enhancing productivity is our only option to thrive in this sector. However, I will elaborate on the challenge of this approach in the following article.
Low productivity is the context of the garment industry in Bangladesh.
Low Productivity: Bangladesh’s garment industry lags far behind all competing countries except Cambodia in terms of productivity (source APO-2020 data). According to the organization’s data, the per capita annual productivity of Bangladeshi workers is 10 thousand 400 US dollars. Whereas Vietnam’s 12 thousand 700 dollars, India’s 15 thousand 800 dollars, and China’s 23 thousand 800 dollars. All the competing countries are ahead of Bangladesh in the international clothing market. Although many discussions and initiatives have been heard for a long time to increase the productivity of factory workers in the country’s export-oriented garment sector, there is no visible progress in reality. Although some government and non-governmental organizations work to improve workers’ skills, it is not enough. Efforts to train industrial owners on their initiative are also not significant. As a result, the fact that Bangladesh is lagging behind the competing countries is emerging.
Low productivity in Bangladesh’s garment industry?
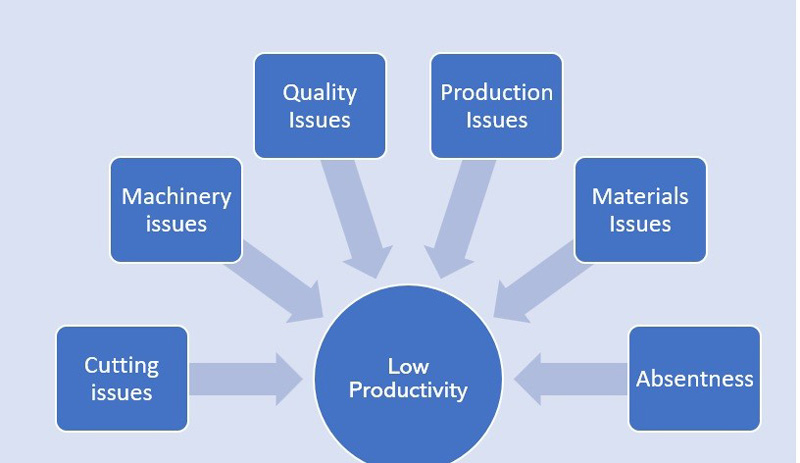
Several factors contribute to low productivity in Bangladesh’s garment industry. Understanding these factors is crucial to developing effective strategies to address this critical issue and improve the sector’s performance. To begin with, one of the main reasons for low productivity in the garment sector is inadequate technology adoption. I will highlight all the reasons in this article. Many factories in Bangladesh still rely on outdated machinery and production methods. This dependence leads to inefficiency and limits the sector’s ability to meet modern production standards.
Low productivity is inadequate adoption of technology:
One of the main reasons for low productivity in Bangladesh’s garment industry is the inadequate adoption of modern technology. Many factories still rely on outdated machinery and production methods. This dependence leads to inefficiencies in the production process, limiting the sector’s ability to meet international quality and efficiency standards. Because we have not yet fully adopted automation, the biggest obstacle to modern technology development is that many old-fashioned people working in garment factories do not want to adopt any technology.
Low productivity is infrastructure constraints:
By infrastructural constraints, we mean a lack of adequate facilities. Insecurate electricity and gas supply and inadequate transport networks are significant challenges for the garment industry. Production delays due to these problems increase costs and hinder productivity. Along with infrastructure development, significantly to reduce traffic jams, the Dhaka-Chittagong double rail line needs to be completed on a priority basis. Political instability is also one of the reasons why investors do not gain confidence.
Low productivity is the reason for Unskilled workers and lack of adequate training.
Bangladesh’s garment industry is dealing with various labor-related that affect productivity. High turnover rates and frequent labor disputes disrupt workflow and create factory unrest. Additionally, the availability of skilled labor is often limited, further hampering productivity as workers may not have the necessary skills to perform tasks efficiently. Besides, the absence of comprehensive employee training programs contributes to low productivity. Many employees lack sufficient skills and knowledge to operate machinery or perform tasks effectively. Investing in continuous skill development can increase productivity by improving the skills and abilities of employees.
Low productivity is the reason for Poor Management Practices.
Inefficient management practices in garment factories also contribute to low productivity. Factors such as suboptimal resource allocation, ineffective planning, and inadequate supervision can cause inefficiencies in manufacturing processes. Applying advanced management techniques and fostering a culture of continuous improvement can increase productivity levels. We cannot equip our mid-level management like that. Our mid-level management is not that efficient. It is not only mid-level management; if we want people today, they can’t even write pure English, let alone pure English. However, the person may have a master’s degree. That is, there is a vast difference between qualifications and requirements. Building mid-level management is challenging because efficient mid-level management does not stand in the factory. Counseling should be done with mid-level management. Keeping in mind the Fourth Industrial Revolution, management should be arranged, and it is necessary to develop the skills of the workers who work in the factory.
Low productivity impacted by poor supply chain system
Bangladesh’s garment sector faces supply chain challenges that affect productivity. Delays in sourcing raw materials and shipping finished products can disrupt production schedules and lead to missed deadlines. Streamlining the supply chain through better coordination and management can mitigate these issues and improve overall productivity. If an inclusive business structure is implemented in the apparel sector, all organizations, big and small, will benefit equally. Gaps in supply chain policies should be identified and addressed through impact measurement. The supply chain needs to be made environmentally friendly to make the apparel industry sustainable. Consumer confidence needs to be strengthened; for this, re-branding of Bangladesh clothing is required.
Low productivity influence by compliance issue
Compliance-related issues often create additional challenges for the apparel industry, disrupting production. Compliance and Regulatory Issues: Compliance with labor laws and international standards. Meeting stringent requirements usually requires extra resources and can affect productivity if not managed effectively. Ensuring compliance while optimizing operations is essential to maintain Production levels. Businesses that fail to comply with regulations can face fines, penalties, and criminal charges. Additionally, non-compliance can damage a business’s reputation and make it difficult to attract customers and investors. In some cases, non-compliance may even result in the closure of a company.
Conclusion
In conclusion, Bangladesh’s garment industry’s causes of low Production are multifaceted and interrelated. Addressing these issues requires a comprehensive approach that includes technology adoption, labour management, skill development, infrastructure improvements, supply chain optimization and effective regulatory compliance. By implementing targeted interventions and creating an enabling environment for growth and innovation, the apparel sector can overcome these challenges and increase its productivity and competitiveness on the global stage.
Author: Abdul Aziz
Head of sample & innovation
Content writer