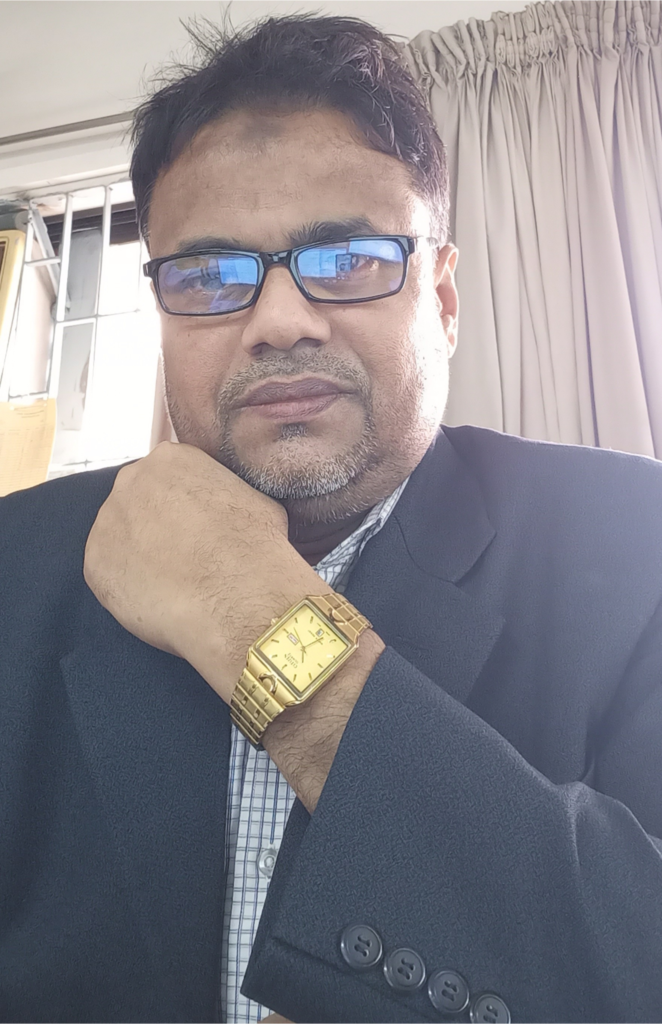
Operational excellence. Learn in detail.
Operational excellence improves efficiency, productivity, quality, and safety throughout a factory’s production operations. It incorporates a holistic approach to continuously improving processes, reducing waste, optimizing resources, and increasing overall performance. Achieving operational excellence requires a combination of lean manufacturing principles, advanced technology, effective management practices, and a culture of continuous improvement. Operational excellence in the increasingly competitive global market is essential for driving the apparel industry’s efficiency, quality, and competitiveness. It involves optimizing production processes, supply chain management, and workforce efficiency to reduce costs and maximize output. By focusing on operational excellence, apparel manufacturers can ensure on-time delivery of high-quality products, maintain customer satisfaction, and quickly adapt to market demands. This approach supports sustainable initiatives by reducing waste and increasing the use of resources.
Operational excellence will protect us from various risks in the apparel industry.
Operational excellence will sustain us from various risks in the apparel industry sector. The garment industry, the main engine of Bangladesh’s economy, is slowly fading away. The first is automation, which is already happening. Different types of machines are coming in, where workers are no longer needed,” the second is changing fashion trends influenced by social media, which significantly impacts clothing brands. And finally, there is the ‘reshoring’ or ‘nearshoring’ of the clothing industry in the final step of automation. That is, from where this garment industry came to countries like Bangladesh, there is a risk of this industry going back there.
Operational excellence and achievement of garment factories.
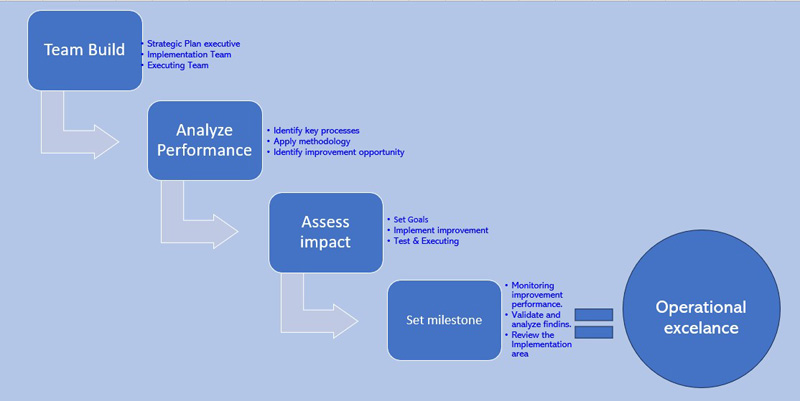
Several tangible benefits are associated with operational excellence and the achievement of garment factories. Which is gradual. Increased productivity: Operational excellence drives efficient workflows, reduces bottlenecks, and maximizes output.
Superior Quality: The factory consistently produces superior-quality garments by streamlining processes and implementing a strict quality control system.
Cost Reduction: Optimized operations lead to lower production costs through reduced waste, efficient resource utilization, and minimal downtime.
Faster time to market: Efficient processes enable quicker turnaround times from design to delivery, allowing the factory to respond quickly to market trends and customer demand.
Increased customer satisfaction: Delivering high-quality garments on time increases customer satisfaction and builds long-term relationships.
Sustainability: Operational excellence often integrates sustainable practices, reduces environmental impact and promotes ethical manufacturing.
Employee Engagement and Satisfaction: Well-organized workflows and supportive management create a positive work environment, increasing employee morale and productivity.
Operational Excellence main components:
1. Lean Manufacturing: This methodology eliminates waste and maximizes value-added activities. It involves just-in-time production, continuous flow, standardized work, and visual management to streamline operations and improve efficiency.
2. Six Sigma: Six Sigma is a data-driven approach to process improvement that aims to reduce defects and variation. It utilizes statistical methods and tools to identify and eliminate root causes of problems, leading to higher quality and consistency in manufacturing.
3. Technology Integration: Leveraging advanced technologies such as automation, robotics, IoT (Internet of Things), AI (Artificial Intelligence), and data analytics is crucial for achieving (OpEx). These technologies enable real-time monitoring, predictive maintenance, and data-driven decision-making.
4. Continuous Improvement Culture: Building a culture where employees at all levels are empowered to suggest improvements, experiment with new ideas, and learn from failures is fundamental to sustained (OpEx). This culture fosters innovation and agility within the organization.
Workflow for .
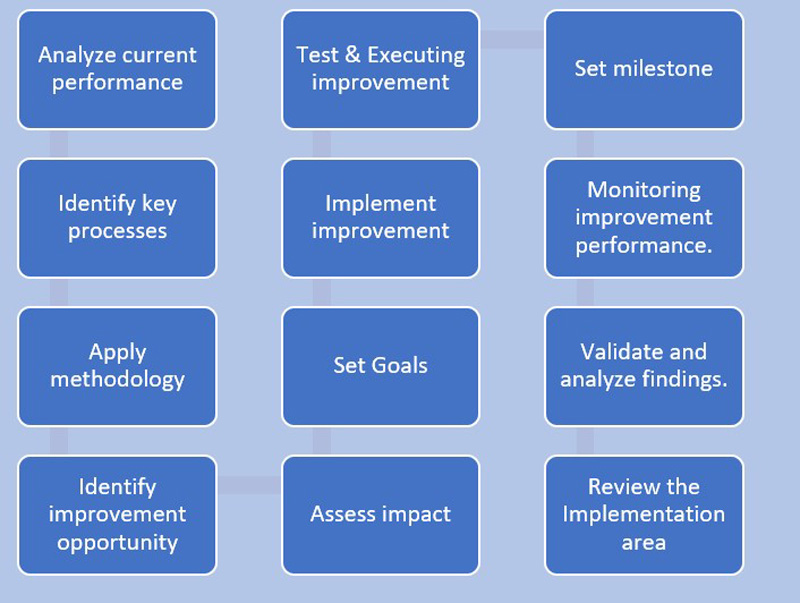
(OpEx) involves optimizing processes to achieve maximum efficiency, quality, and value. The activities are carried out through the following workflows.
Benefits of Operational Excellence in a Factory
1. Improved Efficiency: It to streamlined processes, reduced cycle times, and optimized workflows, resulting in increased productivity and lower costs.
2. Enhanced Quality: (OpEx) ensures higher product quality and consistency by eliminating defects and variation, increasing customer satisfaction and reducing rework.
3. Cost Reduction: Eliminating waste, improving resource utilization, and optimizing inventory levels contribute to significant cost savings throughout manufacturing.
4. Employee Engagement and Satisfaction: Engaged employees in process improvement initiatives feel valued and contribute more effectively to achieving organizational goals.
5. Customer Satisfaction: Higher product quality, on-time delivery, and responsiveness to customer needs increase customer satisfaction and loyalty.
6. Sustainability: It often reduces environmental impact through energy efficiency, waste reduction, and responsible resource management.
Operational Excellence Implementation Challenges:
While the benefits of (OpEx) are substantial, implementation can be challenging and requires commitment from all levels of the organization. Key challenges include:
1. Change Management: Shifting to a culture of continuous improvement requires overcoming resistance to change and ensuring buy-in from all stakeholders.
2. Technology Integration: Adopting and integrating advanced technologies into existing processes can be complex and requires specialized skills.
3. Skills Development: Developing employees’ necessary skills an capabilities to drive and sustain oinitiatives.
4. Measurement and Monitoring: Establishing robust metrics and systems for monitoring performance and progress toward operational goals.
Achieving operational excellence leads to the development of skilled and effective employees..
It will create efficient and competent human resources. There is no alternative to compete in the global market. An institute called BIFT was launched in 1990 to improve the quality of the country’s proud garment industry and overcome the sector’s dependence on foreign manpower. The institute introduced the necessary education system for the textile and garment sector. However, due to the shortage of seats allocated in the institute to ensure the supply of skilled manpower compared to the demand in the garment sector, there was a great speed to meet the shortage of skilled manpower in this sector. Graduate, post-graduate, post-graduate diploma, and certificate programs have been launched in BUFT with the conviction of building skilled and qualified human resources through up-to-date job-oriented education and training for this sector.
Conclusion
Operational excellence in a factory is a strategic imperative for organizations seeking to achieve competitive advantage in today’s dynamic manufacturing landscape. By embracing efficiency, quality, and continuous improvement principles, factories can optimize operations, reduce costs, enhance customer satisfaction, and adapt to market demands. Nevertheless, a successful execution necessitates a holistic strategy that tackles both the technical and cultural facets of transformation. When executed efficiently, operational excellence serves as a foundation for manufacturing success, empowering factories to prosper in an ever-evolving global economy.
Author: Abdul Aziz (Head of Sample & Innovation)
Content writer